- HOME
- 温度・湿度・圧力製品部門
- 技術情報
- 鏡面冷却式露点計によるガス浸炭用熱処理性雰囲気の管理の導入
鏡面冷却式露点計によるガス浸炭用熱処理性雰囲気の管理の導入
鋼部品の表面硬化法
機械類を構成する鋼部品には摩擦部分が多く、耐摩擦製を要求される場合が多い。その場合、鋼炭素の鋼を焼き入れすれば、耐摩擦製は向上するが、材料全体のじん性が低く、疲労限界も低くなり破壊しやすくなる。
強じん性を考えて、炭素量のあまり高くない鋼を用い、焼き入れ後、高温度で焼き戻した鋼は、堅さは低く、耐摩擦性が低い。
このように耐摩擦性とじん性は相矛盾する性質のものであるから、耐摩擦性もよく、じん性もある構造用鋼は得られない。例えばエンジンのカムや歯車などは、粘り強い鋼で作られなければならないが、接触部分とか歯車などは摩耗に耐えることも必要である。
このような2つの要素を満足させる方法として、表面層だけを硬化させ、内部は強じんのまま保つ表面硬化法が用いられる。表面硬化法は耐摩擦性を与えるだけでなく、硬化処理により生じる表面残留圧縮応力によって耐疲労性も向上する効果がある。
表面硬化法としては、
- 1. 浸炭、窒化などのように表面の成分を変化させ硬化する方法
- 2. 高周波焼入、火炎焼入などのように表面のみを焼入、硬化させる方法
- 3. 耐摩擦性の優れた金属を表面に溶着する方法(盛金)
- 4. 表面層のみを加工硬化させる方法(ショットピーニング)
などがある。
ガス浸炭
昭和20年代以降、日本でもガス浸炭の技術が発達した。
ガス浸炭炉では、炉内雰囲気のカーボンポテンシャル(carbon potential)が高くて浸炭性であれば浸炭するし、鋼中炭素量と釣り合えば光輝加熱(bright annealing)が可能で、浸炭も脱炭もしない。カーボンポテンシャルが低ければもちろん脱炭するが、空気中加熱のような酸化物のスケールが発生させることなく脱炭させることができる。
このような雰囲気制御は無公害で経済性も高いので、大部分の浸炭はガス浸炭によって行われるようになってきた。
ガス浸炭は固体浸炭に比べて加熱時間が短く、操作が簡単で、浸炭が均一であり、表面炭素濃度の調節ができるのが特徴である。また、表面が光輝状態で処理でき、浸炭終了後直接焼き入れができる。連続浸炭にも適している。
炭化水素系ガスは全て浸炭性であり、天然ガス(主としてメタン(CH4))、都市ガス、プロパンガス(ブタンガス)、エタン(C2H6)など、いずれも浸炭用ガスとして使用できる。
炭化水素ガスは高温度で分解してススを生じ、これが部品の表面について浸炭を妨げる。その害を除くために、通常、弱浸炭性搬送ガス(キャリアガス)にCH4やプロパン、ブタンなどを少量混ぜたものを送って浸炭を行う。キャリアガスとしてはN2を用いることもあるが、普通には炭化水素と空気を混合してNi触媒で熱分解させたガス(RXガス:CO 20%、H2 40%、N2 40%)を用いる。
浸炭性ガスは恒温に加熱された鋼に接触すると、次のような反応によって分解し、活性炭素を生じ、これが浸炭にあずかる。- 2CO <----> C + CO2 (1)
- CO + H2 <----> C + H2O (2)
- CH4 <----> C + 2H2 (3)
C2H6やC3H8などの高級炭化水素も同様に順次分解して低級炭化水素となり、最後にCH4となる。浸炭性雰囲気ガスはこのようにCO、H2を含むばかりでなく、少量のCO2、H2Oも含み、
- CO + H2O <----> CO2 + H2 (4)
の平行を保ち(水性ガス反応)、水分を除くとCO量が多くなって浸炭性が上昇する。そしてCO/CO2の比によってガスの浸炭性が決定される。もちろん (3) 式によってもある程度浸炭される。
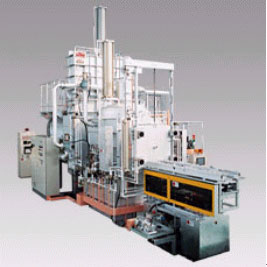
浸炭性雰囲気の露点計測
(4) 式からも分かるように、浸炭性雰囲気のカーボンポテンシャルはその水蒸気分圧に強く依存するので、水蒸気分圧の制御は非常に重要である。この水蒸気分圧の制御は、浸炭性雰囲気ガスの露点計測により行われる。浸炭性雰囲気の露点計測は、ガス浸炭が始まった当初から行われており、長年の経験から露点とカーボンポテンシャルとの間の関係が得られている。
従って、浸炭性雰囲気ガスの露点計測は炉内雰囲気のカーボンポテンシャルを制御する上においては非常に重要となる。
近年ではジルコニアO2センサや赤外線式CO/CO2センサの発達により、センサによるカーボンポテンシャルの直接的な測定を行うケースが増えてきた。また、これらのセンサと連動させて、RXガスの炉内への供給をパルスPID制御することにより、炉内雰囲気のエンリッチコントロールの自動化も可能となってきた。
これらのセンサを使った雰囲気の自動制御システムは、浸炭熱処理現場に大幅な省力化をもたらすものであり、現在では一般的に利用されているものである。しかしこれはセンサの出す値が常に信用できるということを前提としたものである。ところが、ジルコニアO2センサの場合、センサ自体の寿命は非常に短い。また、赤外線式センサの場合も定期的に校正ガス(ゼロガス、スパンガス)による校正を必要としている。さらに赤外線センサでは水をセンサ部に入れてしまうと、簡単に壊れてしまう。特に装置立ち上げ時などの炉内雰囲気の露点が高い場合など、事実上、使用不可能である。
一方、露点計測による場合は上記センサを使った場合のような問題は生じない。どんな場合でも確実に露点からカーボンポテンシャルを得ることが可能である。
従って、浸炭熱処理を行う現場では、通常ジルコニアO2センサや赤外線式CO/CO2センサを使用している場合でも、バックアップとして必ず露点計測を行わなければならない。
しかしながら、浸炭熱処理の現場での露点計測は軽視されているというのが現状である。これはジルコニアO2センサや赤外線式CO/CO2センサが安価で便利であることの他、露点カップによる露点計測が面倒な上に、あまり簡単ではない点に原因があるようにも考えられる。
ISO9000/QS9000と露点計測
-
従来、露点の計測は露点カップを用いて行われてきた。露点カップによる露点計測は、通常は±1℃という精度で露点を計測することが可能であるが、一方で人が露点カップの鏡面の「曇り」を目で見て判断するという点で、個人差がある点に問題がある。また、自動的に計測結果を記録することはできない。近年、浸炭熱処理の現場においてもISO9000の取得を目指すところが増えてきた。開発や生産工程に対するISO9000シリーズの要求する主な項目は次の通りと考えられる。
- 製品の品質チェックではない
- 設計管理 設計の手順や要求事項の明確化
- 実際の仕事のやり方が品質マニュアルに規定された通りか?
・各組織の責任者が書類に明記された作業について理解しているか? - 記録類が品質マニュアルに規定された通りに揃っているか?
・記録類は各工場の品質マニュアルや作業標準書に規定された通りに作られなければならない - 計器管理・データ管理
・各装置のプロセスデータの保管および管理が必要
・国家機関へのトレーサビリティーのとれない計器類では品質の管理はできない
→これによる検査結果は単なる目安としてしか扱われない - 温度センサーや露点計
ISO9000取得の必要条件として温度管理を行う温度センサーは国家計量標準とトレーサブルであることの証明が必要とされている。
ISO9000の取得に際して問題となるのが「計測の正確さ」と「記録」である。「計測の正確さ」を得るためには、各種センサが常に正確に動作していることを証明しなければならない。それが上記ISO9000の要求項目にも示してあるように、定期校正が実施されていることが必須なだけだけでなく、国家計量標準に対してトレーサビリティーがとれていなければならない。
もちろん壊れやすいセンサについては、別の方法によってそのセンサが問題なく動作していることが常に証明できなければならない。従って、浸炭熱処理の現場では、ジルコニアO2センサや赤外線式CO/CO2センサによる炉内雰囲気の分析の他に、別の方法によっても計測のバックアップも必要ということになる。
浸炭熱処理において、雰囲気管理のバックアップとして最も有効であると考えられるものは、露点の計測である。しかしながら、露点カップによる露点計測は前述のような問題点を含んでいる。そこで、この問題を解決するために、近年、鏡面冷却式露点計が浸炭熱処理の現場に導入され始めてきた。
自動露点計測装置は各種存在するが、その中でも鏡面冷却式露点計はJIS規格でも標準湿度計として定義されているだけでなく、センサ部が露点カップを電子化した構造となっていることから、浸炭性雰囲気に大量のススや水分が含まれている場合にも簡単に壊れる心配が無い。そのようなことが理由で、浸炭熱処理、ラジエータなどのアルミろう付け、鉄鋼関係の現場に徐々に普及しつつある。
この鏡面冷却式露点計は、その校正データが日本では工業技術院の計量研究所の湿度標準に対してトレーサビリティーが取れる。1年に1度の校正および記録計による露点の記録と合わせて行えば、ISO9000シリーズの取得に対しては、必要十分な要件を満たすことが可能となる。5.露点カップと露点計との差 実際に鏡面冷却式露点計を使ってみると、同じ気体であっても、露点カップとの間で計測された露点に差があることが分かる。これは、「どの状態が結露している状態か」の判断するポイントが異なるからである。 露点カップでの露点測定では、「鏡面に結露があることが目で見えた状態(結露が発生したあとの状態)」を露点としている。
一方、鏡面冷却式露点計では「鏡面に結露が発生し始める状態」を露点としている。したがって、検出している状態が異なることから、当然露点カップと鏡面冷却式露点計との間では露点が異なる。
しかし、露点の定義から考えると、鏡面冷却式露点計の出す露点がの方が正しいと言える。
露点カップと鏡面冷却式露点計との間でのオフセットは、露点カップでの露点計測が「上手に」行われた場合でも約+1℃のオフセットがある(約+1℃露点カップに比べて鏡面冷却式露点計の方が高く検出される)。過去の露点のデータと、鏡面冷却式露点計によるデーターとを比較する場合には、約1℃のオフセットを考慮しなければならない。
図1- ブタン変成RXガスの露点とCO2量との関係図1はRXガス発生装置におけるCO2と露点との関係を示している。この図は実験的に求められたものである。この図における露点は、露点カップにより求められたものである。弊社での確認実験の結果、この図での露点と実際に鏡面冷却式露点計により求められた露点との間には、約0.8℃(ほぼ1℃と見て良いと思われる)のオフセットがあったことが確認された。
鏡面冷却式露点計導入のすすめ
-
ISO9000導入を念頭に置いて浸炭熱処理プロセスの品質管理を考えた場合、ジルコニアO2センサや赤外線式CO/CO2センサが完璧であるとは言えないだけに、バックアップ計器として鏡面冷却式露点計のご導入の検討を弊社ではお勧めしております。
弊社では、露点計測はガス浸炭熱処理における雰囲気コントロールの基本であると考えております。浸炭熱処理の現場の品質管理にもISO9000の導入機運が高まっていることを機に、鏡面冷却式露点計のご導入と、これによる品質管理体制の確立をお勧め致します。
鏡面冷却式露点計 DewStarシリーズ
【参考文献】
講座・現代の金属学 材料編4 鉄鋼材料,「8.鋼の表面硬化法」,田村 今男・牧 正志,日本金属学会,1985年
金属工学シリーズ1 構成金属材料とその熱処理,「15.表面硬化法」,門間 改三・須藤 一,日本金属学会,1977年
JIS Z 8806-1995 「湿度−測定方法」, 日本規格協会発行,平成7年12月1日改正
JIS Z 7920-1994 「湿度計−性能試験方法」, 日本規格協会発行,平成6年3月1日制定